As a manufacturer of seals, we recognize the importance of ensuring your seals are as durable as your equipment. If you do not find the solution you need in this passage, please reach out to our expert team for assistance. Here're some common reasons for seals failure and tips to help extend their lifespan.
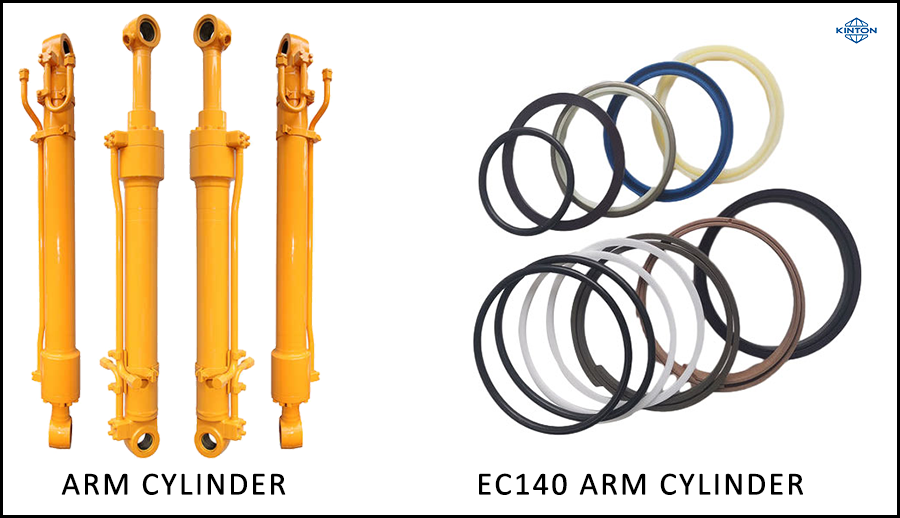
Improper Installation
Since there are no formal qualifications required for mechanical seal installation, improper techniques often lead to premature seals failure. Even minor errors, such as scratching the seal during installation, can cause issues. This is why experience is highly recommended. Adhering to proper procedures and using the correct installation tools significantly impacts both the longevity and effectiveness of your seals.
Overheating
Seals can overheat primarily due to insufficient lubrication and excessive friction. Overheating is often caused by:
1.Inadequate lubrication to dissipate heat generated by the seals. Increased oil temperature from other system components reduces oil viscosity, leading to decreased lubrication efficiency.
2.Using the wrong type of lubricating oil.
3.Excessive friction caused by surface scratches or scoring during installation, which increases heat generation.
4.Over-compression of O-rings, leading to higher loads on the seals and increased friction.
5.Improper surface finish on seals, which also contributes to higher friction levels.
Incorrect Seal for the Application
If a seal fails prematurely without an obvious cause, it may be due to a manufacturing defect or the use of an incorrect seal for the application. In such cases, investing in a high-quality, reliable seal is crucial, as the cost of a poor-quality seal far outweighs the initial savings. We offer a wide range of seal kits tailored to various needs like EC140 arm cylinder seal kit. If you encounter this issue, please consult our professional engineers or sales representatives for support.