Hydraulic seal is crucial in industrial settings, playing a pivotal role in equipment by preventing liquid or gas leakage. Choosing the right seals is essential for ensuring the efficiency and reliability of hydraulic systems. This guide provides a structured approach to selecting hydraulic seals:
Step 1: Understand System Requirements
Before selecting hydraulic seals, thoroughly grasp your system's operating conditions, including temperature, pressure range, working medium, and speed.
Step 2: Determine Seal Type
Hydraulic seals vary by type, such as dust seals, rod seals, piston seals, guide rings, and O-rings like VOE 14508911 ring. Select based on application and motion type (reciprocating or rotary).
Step 3: Select Seal Material
Choose materials like PTFE, NBR, PU, or FKM like 1261937 Seal Kits based on compatibility with hydraulic media, temperature range, and resistance to abrasion and chemicals.
Step 4: Determine Seal Size
Select seal dimensions that match equipment specifications, considering rod and piston diameters, bore dimensions, seal heights, and groove sizes for effective installation and sealing.
Step 5: Prioritize Quality and Reliability
Emphasize seal quality over cost by opting for reputable brands with ISO 9001 certification. High-quality seals reduce maintenance costs and downtime, ensuring long-term efficiency.
Step 6: Validate and Test
Conduct rigorous testing under operational conditions to assess wear, heat effects, and reliability. Validate compatibility with hydraulic fluids to ensure seal longevity.
In summary, selecting hydraulic seals involves considering factors like material properties, environmental conditions, operating pressures, and seal geometry. By carefully evaluating these elements, you can choose seals that optimize hydraulic system performance and reliability.
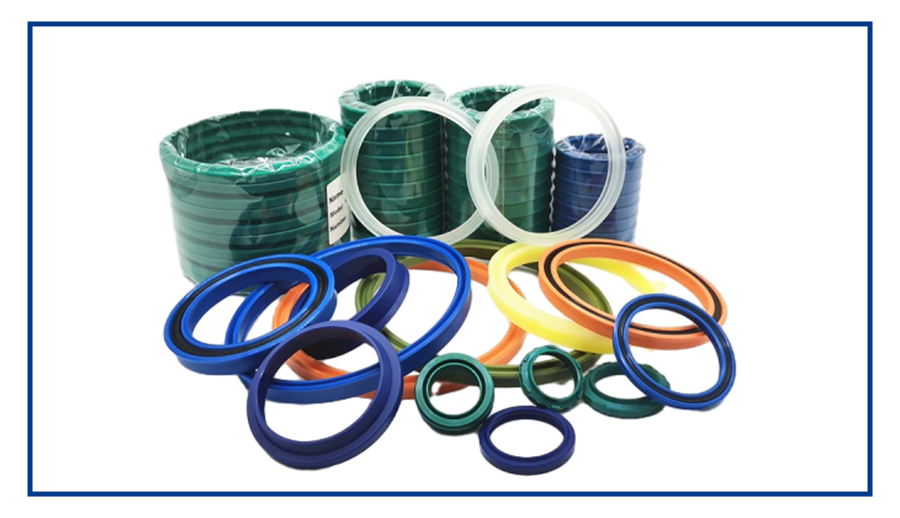